Why do prototype products make surface treatments?
Improve the appearance quality: Making surface treatments will make prototype products more beautiful and fantastic!
Enhance product durability: Some surface treatments can improve the hardness, wear resistance and corrosion resistance, thereby enhancing the service life and durability of products.
Realize special functions: For example, electroplating technology can realize conductive function, spraying technology can realize a specific color or texture, and printing technology can print specific patterns or logos on products.
Huachen Precision not only could do machining but also finish all surface treatments for you after machining. Our one- stop service could save your time and total cost.
The below are some surface finished parts to share with you. If you need more, you could enquire our sales team anytime.
Brushing
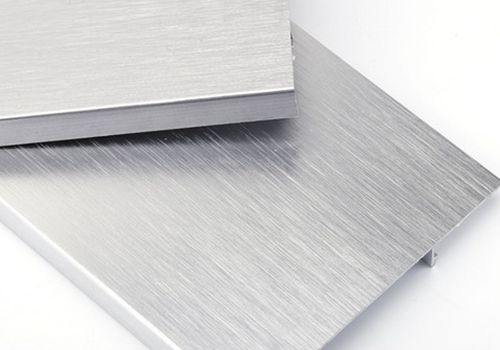
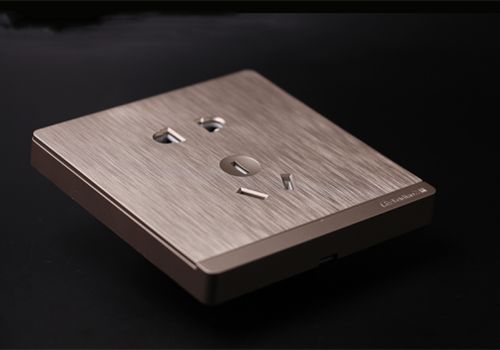
Brushing is produced by polishing the metal with grit resulting in a unidirectional satin finish. The surface roughness is 0.8-1.5um.
Application:
Home appliance panel
Various digital product peripherals and panels
Laptop panel
Various signs
Membrane switch
Nameplate
Polishing
Metal polishing is the process of using abrasive materials to smooth and shine metal surfaces. Whether you work in architecture, automotive, marine, or another industrial sector, it’s important to make metal polishing a part of your process to remove oxidation, corrosion, or other contaminants that might tarnish the appearance of your metal surfaces.
This type of high performance surface with little roughness is required above all in medical technology, turbine and transmission manufacturing, the jewelry industry and the automotive industry. Polishing work pieces can optimize the resistance to wear and tear and minimize the energy consumption and noise.
Polishing technology is widely used in mechanical parts, electronic components, stainless steel parts, medical equipment, mobile phone accessories, precision parts, electrical components, instrumentation, light industry, aerospace military industry, auto parts, bearings, tools, watches, bicycle parts, small and medium precision workpieces in motorcycle parts, metal stamping parts, tableware, hydraulic parts, pneumatic parts, sewing machine parts, handicrafts and other industries.
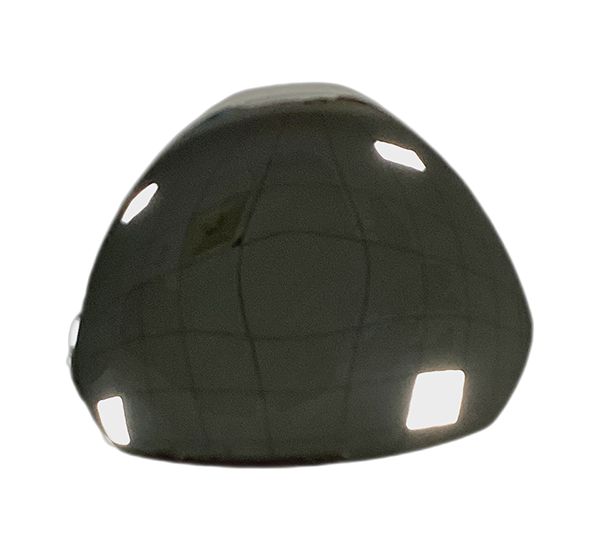
Vapor Polishing-PC
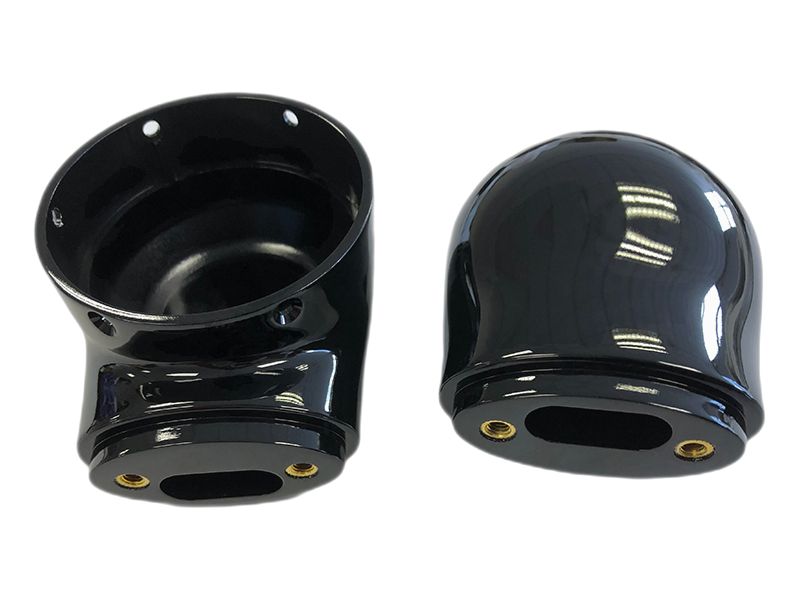
This is a specialized treatment we do in-house for achieving optical clarity or glossy effect on polycarbonate (PC) plastic. This method can also be used for repairing minor surface defects and is ideal for achieving an extremely clear surface or glossy effect on complex geometries or hard-to-reach areas. After carefully preparing the part with sanding up to #1500 grit, it is then placed in an atmospherically controlled environment. Weldon 4 gas is used to melt the surface of the plastic at the molecular level, which rapidly reforms with all microscopic scratches blended out.
Glossy High Polishing-Specific Plastics
By polishing the edges of this material and other types of plastics such as polycarbonate, acrylic, PMMA, PC, PS, or other technical plastics, even aluminum, the workpiece is given much more light, shine, smoothness, and transparency. With shiny edges and free of marks created by the cutting tools, the methacrylate pieces get greater transparency, where an added value to the piece.
The surface finishing through polishing requires not only specially designed process technology if the piece is to reach its optimal function and life span. This final treatment also embosses the product with the quality seal of the processor. Because very smooth and/or high-shine surfaces are a sign of proven aesthetics and quality.
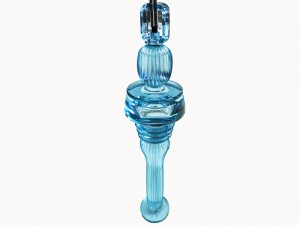
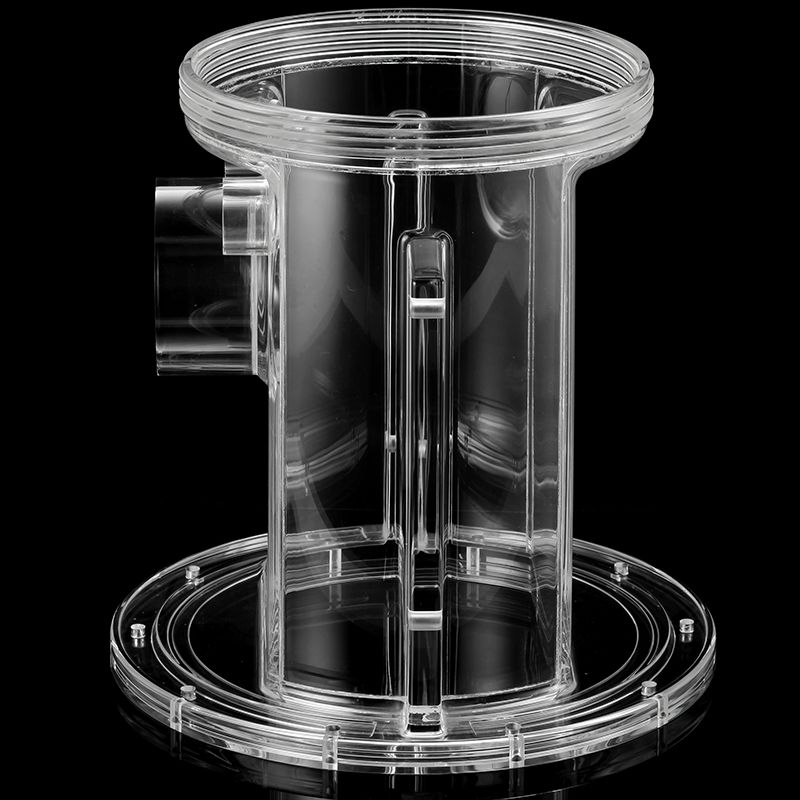
Anodized-Aluminum
(Bead)SandBlasted+Anodized
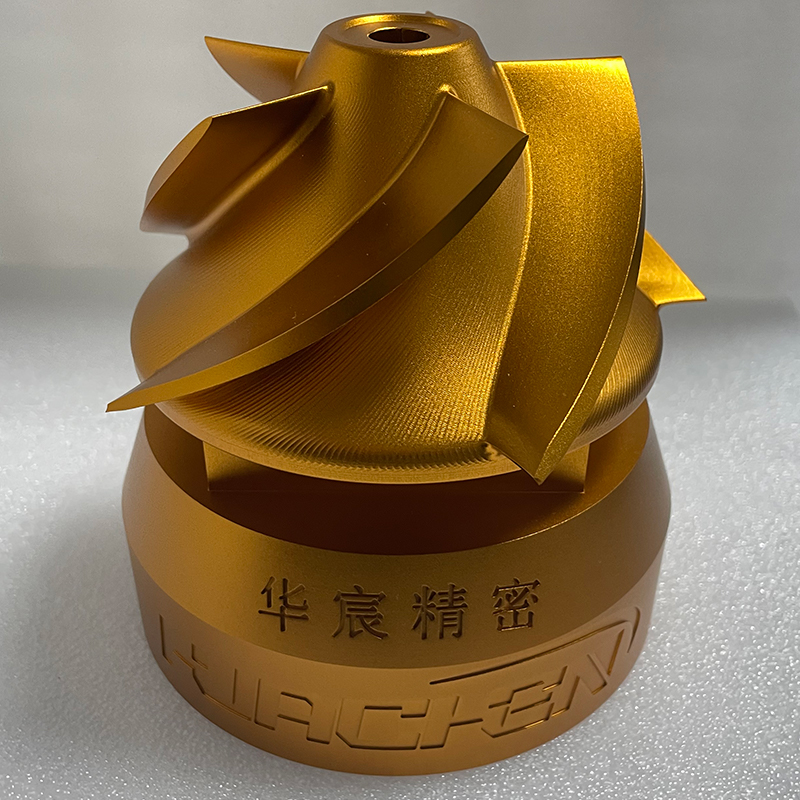
Anodizing offers a large increasing number of gloss and color alternatives and minimizes or eliminates color variations. Unlike other finishes, anodizing allows aluminum to maintain its metallic appearance. A lower initial finishing cost combines with lower maintenance costs for more excellent long-term value.
The Benefits of Anodizing
#1) Corrosion Resistance
#2) Increased Adhesion
#3) Lubrication
#4) Dyeing
Notes:
1) Color matching can be carried out according to RAL color card or Pantone color card, while there is an additional charge for mixing color.
2) Even if the color is adjusted according to the color card, there will be a color aberration effect, which is inevitable.
3) Different materials will lead to different colors.
Blackening/Black Oxide-Steel
Black Oxide Process is a chemical conversion coating. This means that the black oxide is not deposited on the surface of the substrate like nickel or zinc electroplating. Instead, Black Oxide Coating is produced by a chemical reaction between the iron on the surface of the ferrous metal and the oxidizing salts present in the black oxide solution.
Black Oxide is deposited on materials mainly to protect against corrosion and also has somewhat lowered reflectivity. In addition to their overall superior low-reflectivity performance. The Black coatings can be tailored for specific spectral requirements. The oil or wax impregnates in black oxide coatings make them unsuitable for vacuum or elevated temperature applications because of outgassing considerations. For the same reason these coatings cannot be space qualified. Black Oxide can be tailored – within limits – to electrical conductivity requirements. Metal that undergoes black oxide conversion also receives two more distinct advantages: dimensional stability and corrosion resistance. After black oxide, parts receive a supplemental post treatment of a rust preventative.
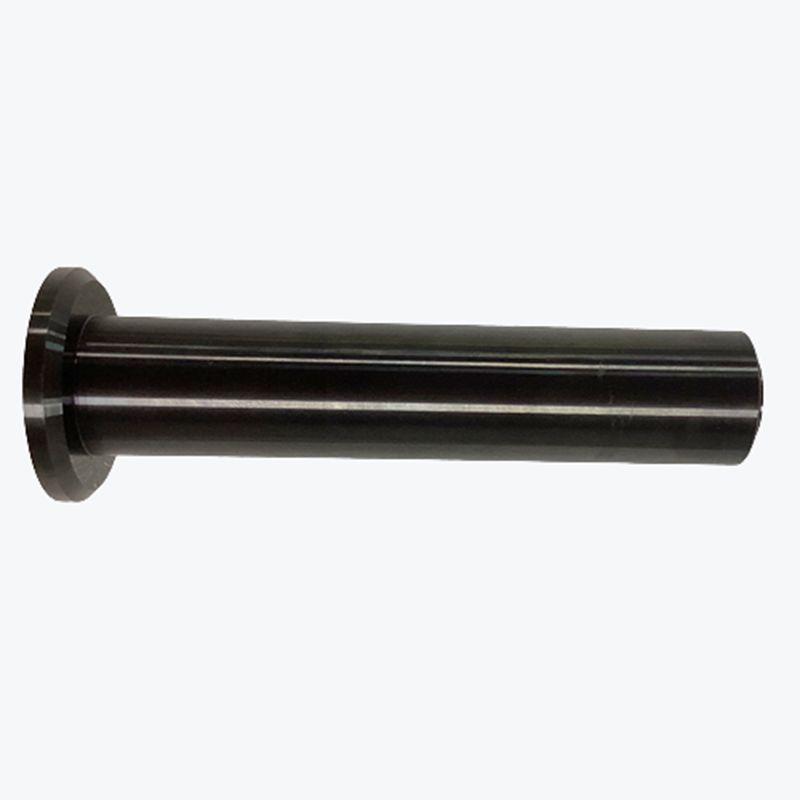
Chromate Conversion Coating (Alodine/Chemfilm)
Chromate conversion coating is used for passive metals using an immersion bath process. It is primarily applied as a corrosion inhibitor, primer, decorative finish or to retain electrical conductivity and usually imparts a distinctively iridescent, greenish-yellow color to otherwise white or gray metals.
The coating has a complex composition including chromium salts and a complex structure. It commonly applied to items such as screws, hardware and tools.
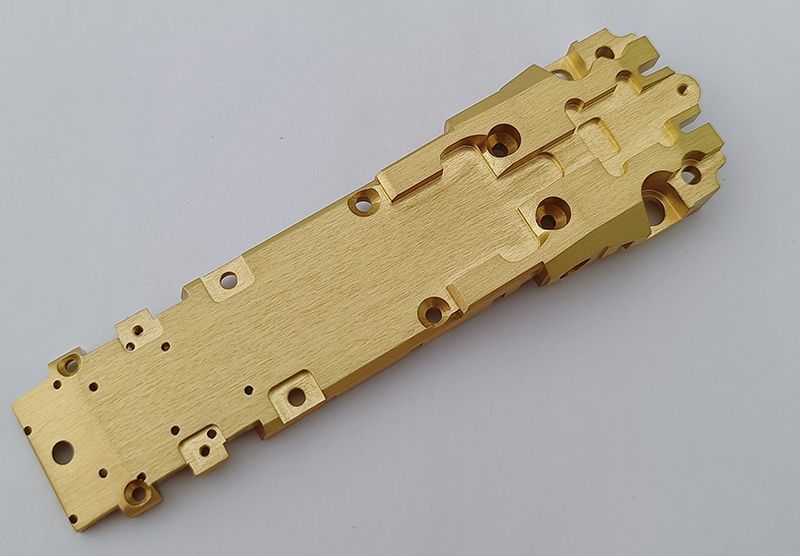
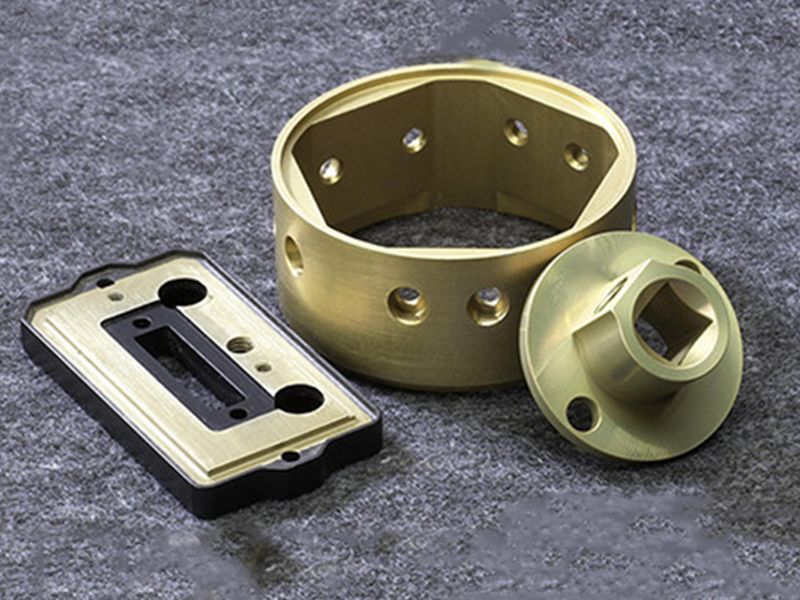
Laser Engraving(Laser Etching)

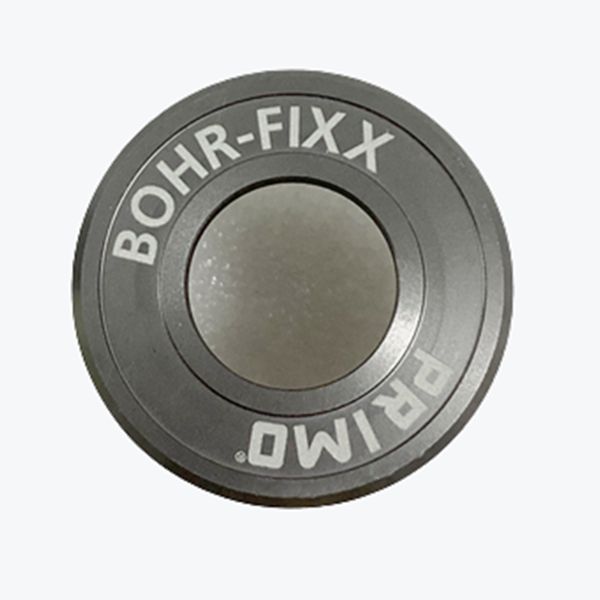
Laser engraving is the most popular laser marking technology in product identification and traceability. It involves using a laser marking machine to make permanent markings on different materials.
Laser engraving technology is highly accurate. Consequently, it is the go-to option for marking parts and products in many industries, especially automotive and aeronautics.
Plating
Electroplating lets you combine the strength, electrical conductivity, abrasion and corrosion resistance, and appearance of certain metals with different materials that boast their own benefits, such as affordable and/or lightweight metals or plastics. The coating can enhance the corrosion resistance of the metal (the coating metal mostly adopts corrosion-resistant metal), increase the hardness, prevent abrasion, improve the conductivity, smoothness, heat resistance and beautiful surface.
Materials commonly used in electroplating include:
Brass
Cadmium
Chromium
Copper
Gold
Iron
Nickel
Silver
Titanium
Zinc
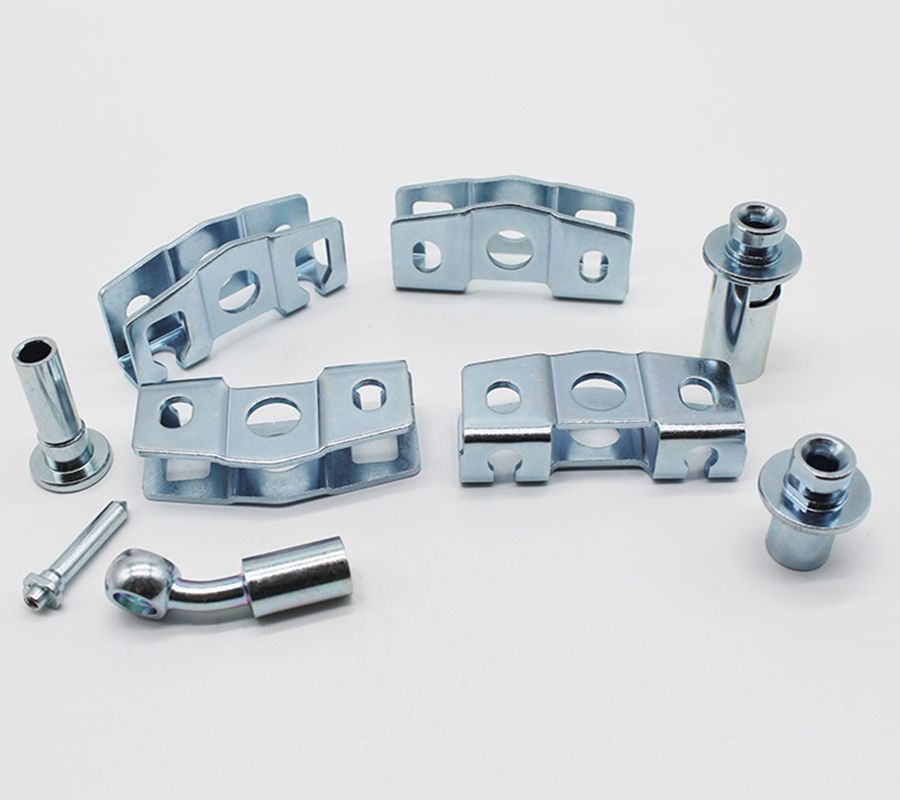
Spray Painting
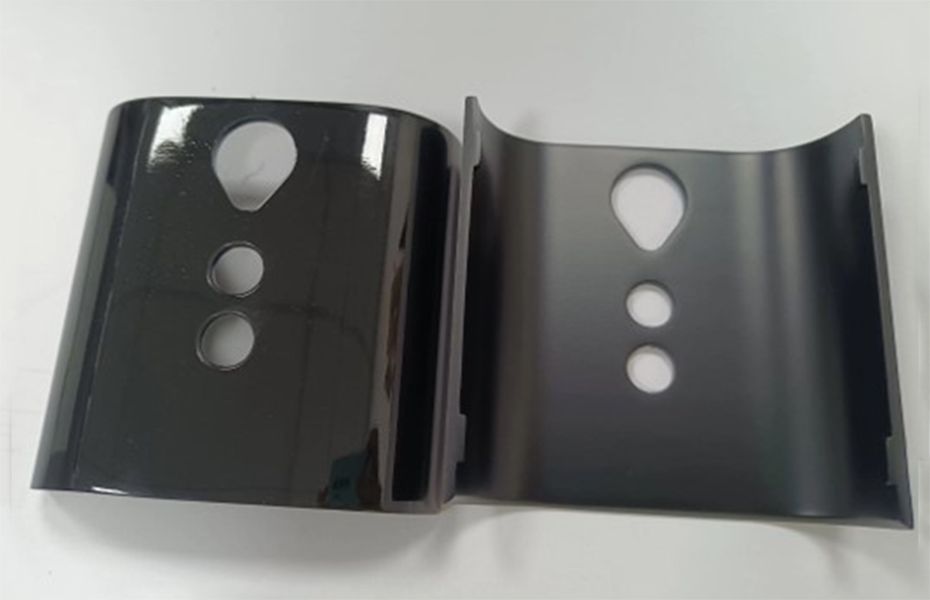
Spray painting is a far quicker job to carry out in comparison to brush painting. You can also reach areas you cannot with a brush, the coverage is better, the finish is better and there are no brush marks or bubbles or cracks remaining on completion. Surfaces that have been primed and prepared correctly prior to spray painting will last longer and are more durable.
Industrial spray painting provides a fast and economical way to apply high-quality paint coatings to a wide range of surfaces. Here are our top 5 benefits of industrial spray painting systems:
1. range of applications
2.speed and efficient
3. controlled automisation
4. less waste
5. better finish
Silk-Screen
Silk-screen is a layer of ink traces used to identify components, test points, parts of the PCB, warning symbols, logos and marks etc. This silkscreen is usually applied on the component side; however using silkscreen on the solder side is also not uncommon. But this may increase the cost. Silkscreen can help both the manufacturer and the engineer to locate and identify all the components. The color of printing can be changed by adjusting the color of paint.
Screen printing is the most common surface treatment process. It uses a screen as a plate base and uses photosensitive plate-making methods to produce printing effects with graphics. The process is very mature. The principle and technological process of silk screen printing are very simple. It is to use the basic principle that the graphic part of the mesh is transparent to ink, and the non-graphic part of the mesh is impermeable to ink. When printing, pour ink into one end of the screen printing plate, apply a certain amount of pressure on the ink part of the screen printing plate with the scraper, and at the same time, print towards the other end of the screen printing plate. The ink is squeezed by the scraper from the mesh of the graphic part to the substrate during the movement.
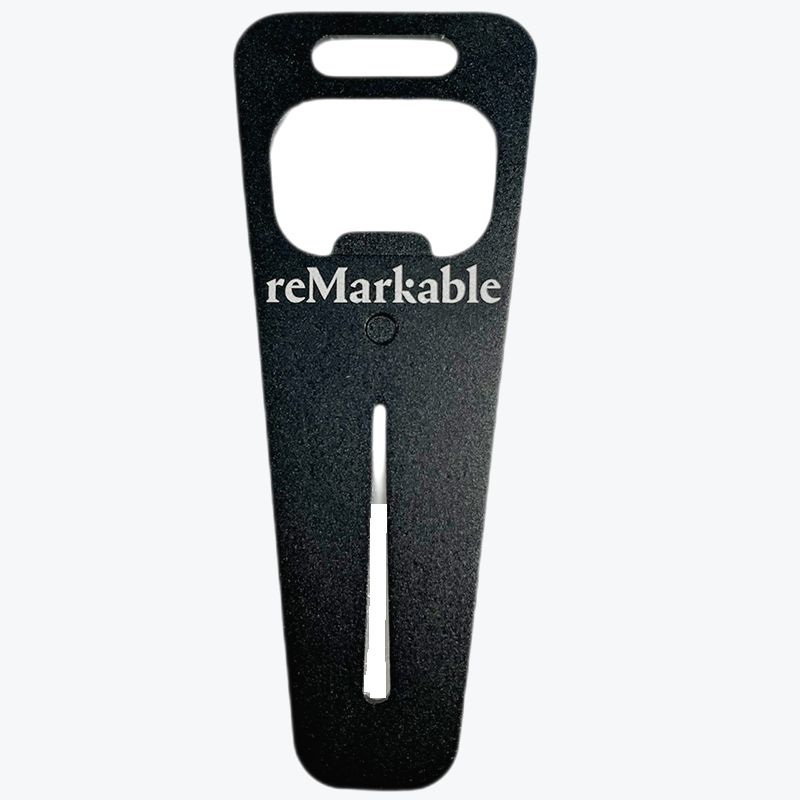
Powder Coating
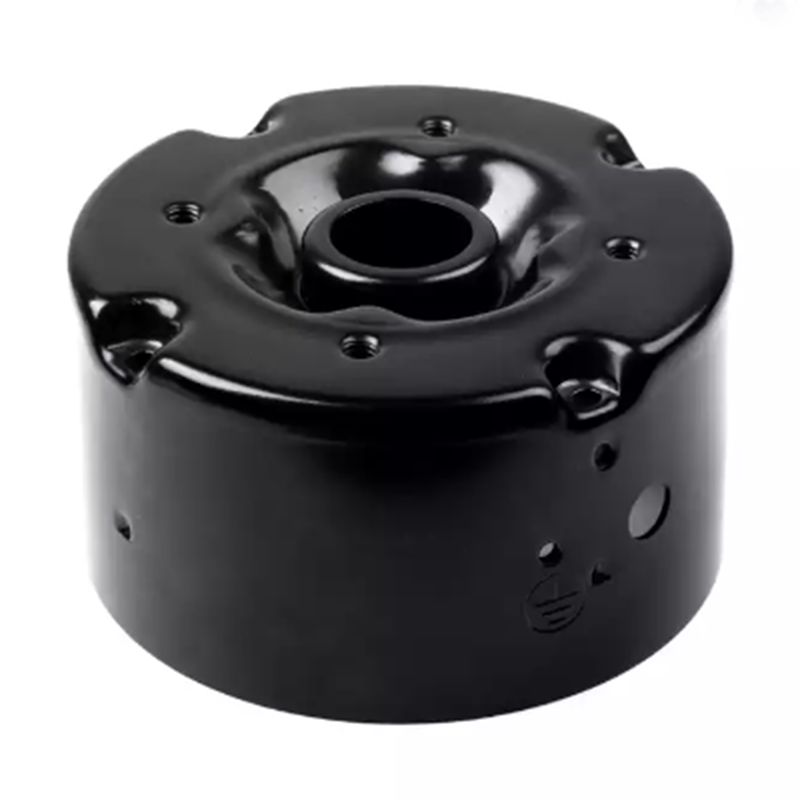
Powder coating is a high-quality finish found on thousands of products you come in contact with each day. Powder coating protects the roughest, toughest machinery as well as the household items you depend on daily. It provides a more durable finish than liquid paints can offer, while still providing an attractive finish. Powder coated products are more resistant to diminished coating quality as a result of impact, moisture, chemicals, ultraviolet light, and other extreme weather conditions. In turn, this reduces the risk of scratches, chipping, abrasions, corrosion, fading, and other wear issues. It is widely used in hardware products.
Notes:
1) Color matching can be carried out according to RAL color card and Pantone color card, but there is an additional charge for mixing color.
2) Even if the color is adjusted according to the color card, there will be a color aberration effect, which is inevitable.